Water opportunities in manufacturing
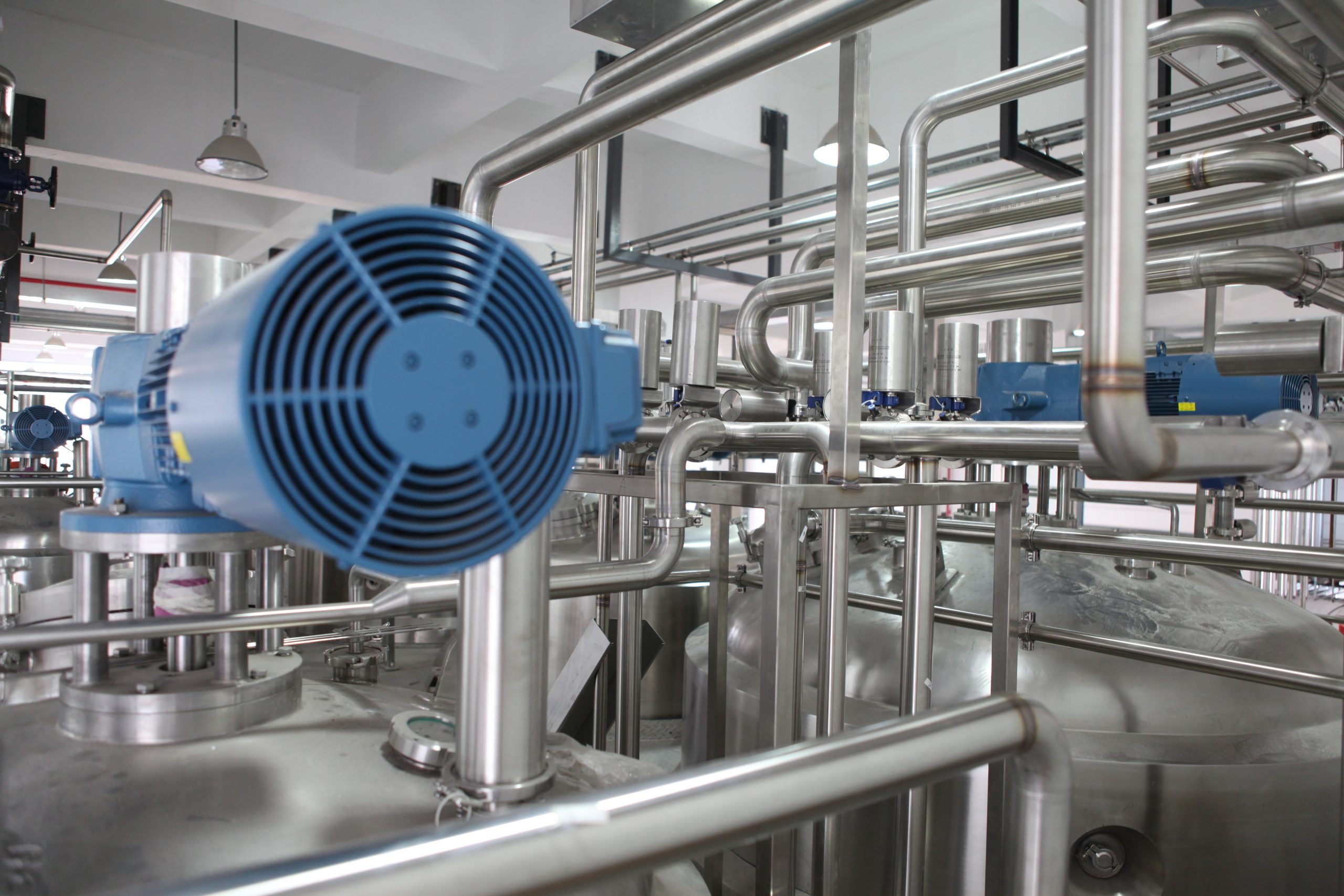
MBB, EWA & The Malta Chamber are offering guidance to manufacturing companies to become more water efficient in their operations. Hosting a webinar on Water in Manufacturing, the institutions invited three leading manufacturing companies to showcase their best practices on water efficiency to the business community. The event therefore served to provide ideas and inspiration to other manufacturers on what sorts of innovations are possible as regards water efficiency. Within the scope of the WE MAKE project, the institutions therefore offer support in identifying financing opportunities to implement such projects, such as the Smart & Sustainable grant offered by Malta Enterprise.
Timothy Alden, Senior Projects Executive for Sustainability at MBB, stated that water management is expected to take a more pronounced role among the metrics for sustainability going forward, and as Malta’s water resources come under increasing strain, efficiency will become increasingly urgent from both a sustainability and business perspective.
Deputy President of The Malta Chamber, Chris Vassallo Cesareo indicated that water efficiency is an important component of a competitive cost-base, and that the project is attempting to address the broad applications of water to industry.
CEO of EWA, Manuel Sapiano, stated in an opening speech that there is an important link between water and energy efficiency, and that they should not be seen in isolation. Water which is saved is ultimately translated in energy savings, just as water may need to be efficiently heated in turn as processes dictate.
Seifert, Toly and Trelleborg each gave a presentation on their water systems. Seifert unveiled its plans to create two major reservoirs, and plans to use the water for, amongst other things, surface treatment equipment used for sheet metal. They have used estimations of precipitation to calculate their pay-offs from the planned reservoirs, with potential net positive cumulative effects across the years. Furthermore, Seifert is using automation and new equipment to ensure less water is used, and leakages are easier to detect and repair.
Toly’s underground reservoir is utilised for both process water and for heating/cooling, and heat exchangers separate the two types of water which removes the need for treatment. The reservoir is replenished by rainwater harvested from the roof. It captures wastewater from chillers and air-conditioning units for process water. The process water is used in a closed loop system, preventing wastage through individually controlled optimize high flow process pumps. Toly is now planning a project to capture reverse osmosis wastewater for domestic use, and to install flow meters to capture data regarding harvested water.
Trelleborg’s water system uses chilled water only where it is strictly necessary within the company’s operation. Second class water is used for sanitary purposes, to cool hydraulic equipment and for one of Trelleborg’s processes. The reservoir is segregated so as to trap debris and prevent it from flowing into the rest of the system, and for availability for use in case of a fire. The process water is mostly used for centrifugal finishing, which entails tumbling unfinished rubber seal products inside a rotating tub with ceramic media, and a continuous flow of water. The desired outcome is the creation of friction, and the water ensures that there is no overheating destroying the product. The water used in this near continuous process is left with undissolved ceramic waste content, but once it settles, the water is clear and may be reused. Therefore, Trelleborg set up a water treatment plant for its process water, which has significantly reduced overall water consumption. In future, particularly with a planned new manufacturing campus extension of the company, Trelleborg intends to develop another reservoir, water recycling plant, an increase in metered points, and it plans to extend the use of second-class water.
Bringing in an institutional perspective, the workshop had the Water Services Corporation showcase investments in national water infrastructure and wastewater treatment and reuse, and the expansion of reservoirs. The workshop concluded having tied together the various opportunities and uses for water in manufacturing in Malta.
The WE MAKE project is planning another event on private financing instruments and green loans as the subject of its next workshop on 23rd March at 10:00hrs.
The Water and Energy Management and Knowledge Transfer in Manufacturing Enterprises (WE MAKE) project, is a collaboration between the Malta Business Bureau and The Malta Chamber, sponsored by EWA, to give manufacturing industry businesses guidance on how to consume energy and water efficiently. Those interested in receiving these services should get in touch with MBB at talden@mbb.org.mt