The Value of Energy Monitoring in Manufacturing
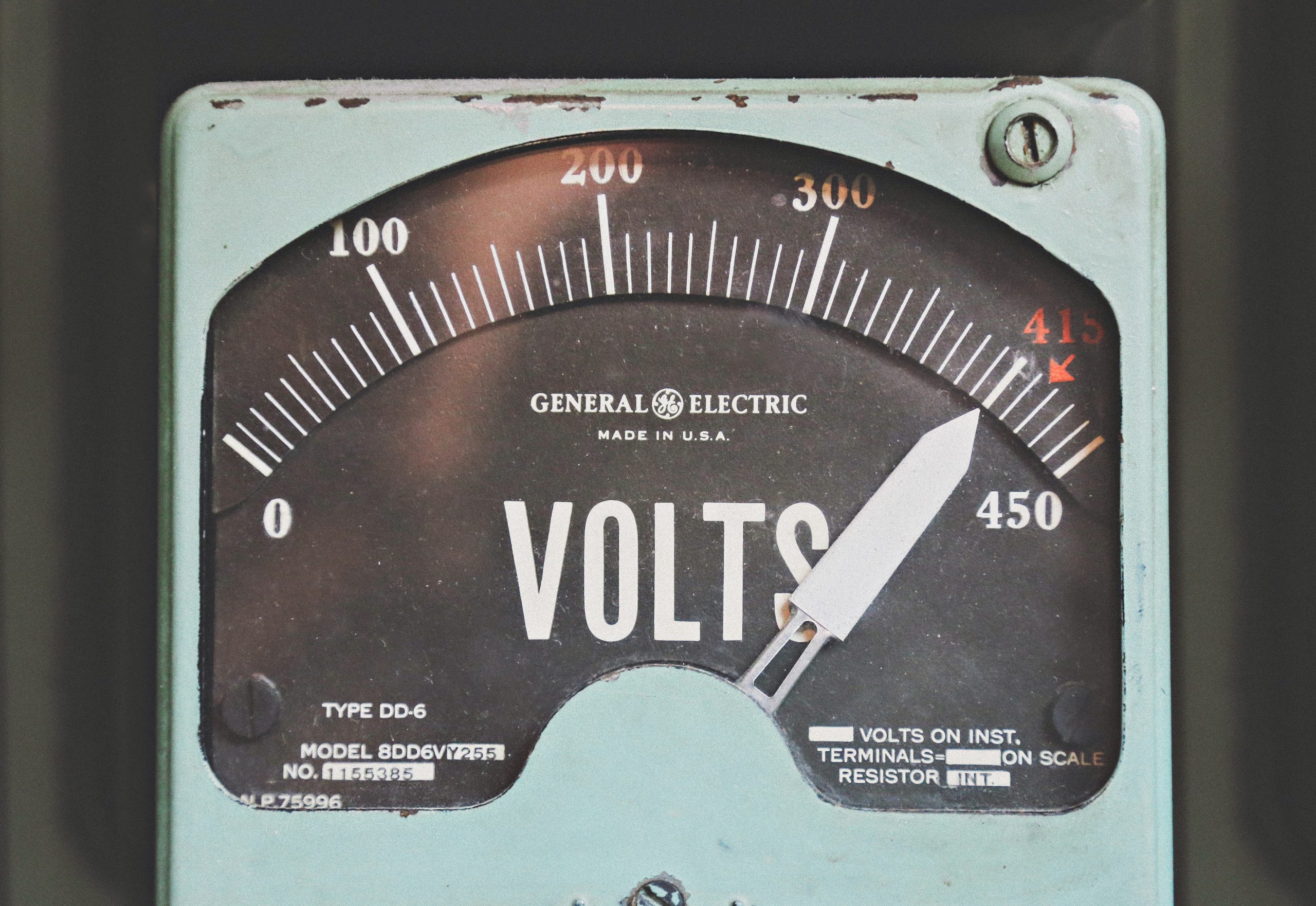
Press Release
EWA, MBB & The Malta Chamber hosted a session on Energy Monitoring in Manufacturing, bringing together institutions and leading businesses to share best practices and highlight funding opportunities. STMicroelectronics and Seifert showcased their energy monitoring systems in operation, indicating the savings obtained and the procedures and best practices. Malta Enterprise and the Measures & Funds Division afterwards explained some key funding opportunities of direct relevance to energy monitoring. This is the sixth event of the WE MAKE project, an initiative established to encourage the uptake of energy efficiency measures in local manufacturing companies.
Incorporated into the discussion, the companies covered ISO as one of the topics. STMicroelectronics showcased its ISO 50001 management system. It provides requirements for establishing, managing, and improving energy consumption and efficiency. It is designed to be compatible and harmonised with other similar standards such as ISO 14001, which Seifert possesses. ISO 50001 assists facilities in the evaluation and prioritization of new technologies and better handling energy use and consumption, creating transparency and improved communication. It also entails a framework for increased energy efficiency through the supply chain. STMicroelectronics also emphasised the importance of internally set KPIs, energy meters and best practices such as weekly monitoring procedures and comparing consumption with production. With a target of being carbon neutral by 2027, STMicroelectronics is considering not only Scope 1 emissions, but also Scope 2 & 3, which imply that the company considers not only its direct emission but also those in its value chain.
Seifert’s journey towards greener operations results from various energy monitoring initiatives. Its targeted monitoring activities, such as on specific machines such as its vacuum furnace and compressed air system, allowed the company to identify how one old machine alone accounted for 19.5% of the company’s annual energy bill. As a result, the company opted for a new machine system. Through application of Industry 4.0 principles, a new intelligent sheet metal management system by Seifert will allow full traceability of components and resources and enable the most efficient possible operation. Scrap and waste will be minimised due to the optimal nesting system. Seifert’s ISO 9001 and ISO 14001 certification are a core component of their process of continuous improvement.
Having provided inspiration for project ideas and improvements, the WE MAKE project then invited Malta Enterprise and the Measures & Support Division to showcase their schemes. Between them, there was scope to pursue sustainable digitalisation. In other words, the implementation of energy monitoring systems or Industry 4.0 software to increase efficiency and thus also competitiveness. Further information may be found on their respective websites.
Aiming to hold a monthly workshop from now until the end of July, the WE MAKE project continues to bring together key players in industry to offer an innovative vision towards greener industry.